MEASURE PHASE
Phase two of five progressive phases

PHASE SUMMARY
The main goal of this phase is to identify the status quo for harvesting Oil Palm fruits. The team will collect data on what the current process is, how much money is spent, how much time is being used, how well the process performs, if there are any inefficiencies, and if variation is within acceptable levels. The team will also develop, evolve, and finalize a project design. This design will be compared to the current standard in the Oil Palm industry and the previous year’s design to ensure that the new design is an improvement.
ESTABLISHING BASELINE PERFORMANCE
There are two main methods that are implemented in today’s world to harvest Oil Palm fruit from an Oil Palm tree. Both methods are problematic in that they dangerous and time consuming. For one of these methods, a worker must climb the tree only using a strap to prevent him from falling to the ground. For the other method, a worker uses a very long pole with a saw-like blade on the end to cut the fruit down. These methods are extremely dangerous and take an extensive amount of time, resulting in a higher cost for plantation owners. Also, there is very little standardization in the process. There is great variation from each worker’s skill and physical strength, and this is further affected by how they perform on and throughout a particular day. The Oil Palm Harvester would revolutionize the process. It would decrease the time required to harvest fruit, mitigate the associated dangers, and reduce variation in the process which will increase productivity and save the owners money. tree.
​
The most problematic aspects of the current Oil Palm Harvester prototype are the substantial weight of the mechanism and the lack of stability when the elevation system is extended. The previous year’s Senior Design team changed their Oil Palm Harvester’s elevation mechanism to an Aluminum 6063 squared cross-section with the purpose of increasing its yield strength and improving the stability of the structure. However, these changes were not enough to significantly decrease the weight and increase the stability of the mechanism. This renders the mechanism ineffective for real-world application. The device also did not have the proper height capabilities, as it was only able to reach a height of 25 feet. The improved device will address this issues by using a T-Shapped cross section rather than square cross section, which will reduce the material used and decrease the weight of the mechanism. The device will also be more stable by being able to lock in place on the tree once it is extended. Finally, the device will also have increased height capabilities of 40 feet so that it will be more useful in application.
THE FINAL DESIGN
It was established that the improved design would have an elevation mechanism composed of six seven-foot-long aluminum poles attached to a system of pulleys. The pole would be made of T-Slotted aluminum beams. This new elevation mechanism will give the mechanism the required height capabilities, and will increase its mobility because it will be able to retract to a height of seven feet. The use of aluminum translates into a lightweight product that is cost-effective. Since this mechanism will be able to reach higher than the previous year’s mechanism, legs will be added to the base to make the device more stable. The device will also lock in place around the tree when extended for additional stability. These changes will allow for the device that accomplishes the project objectives. The device's design is pictured below.
OIL PALM HARVESTER CAD
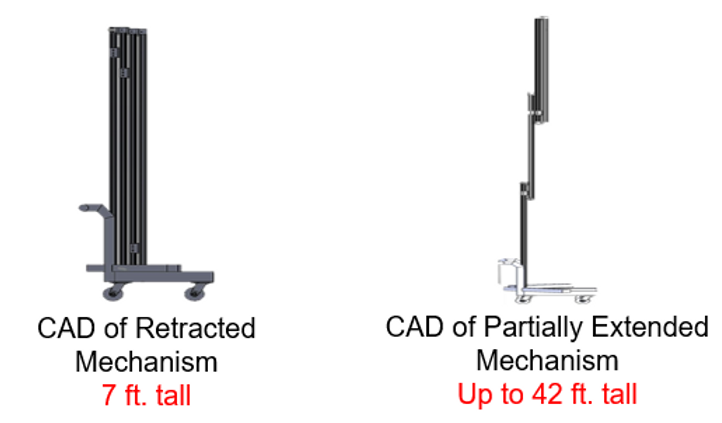